Manufacturing Excellence in Motion: Lessons from Jaguar Land Rover
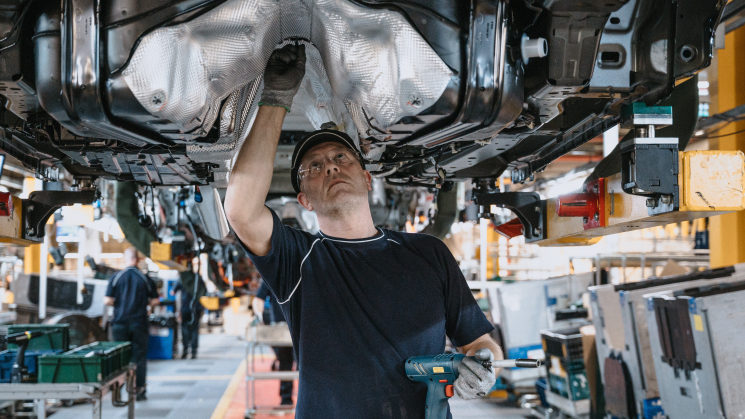
Just imagine… walking through a manufacturing plant so advanced, it feels like you’ve stepped into the future. That’s exactly what we experienced on our recent visit to Jaguar Land Rover (JLR). But what struck us wasn’t just the cutting-edge tech or precision engineering – it was the way every decision, every process, every tool was aligned behind a bold vision.
At HURST, we love learning from businesses who are doing great things – especially when those lessons can help our clients. Here’s what stood out, and how it could inspire better thinking in your business.
1. Circular manufacturing done right
Sustainability isn’t a buzzword at JLR – it’s business-critical. Their commitment to circular manufacturing is already delivering results: over £100 million saved through reusing, refurbishing and recycling equipment. More than 50,000 square metres of production assets brought back into use. It’s clever, efficient, and future-focused.
Takeaway for leaders: Think beyond compliance – how can you build a circular mindset into your own operation to cut costs and boost resilience?
2. Owning the process
We were impressed by JLR’s decision to bring key manufacturing processes back in-house – including a £1.7m investment to produce press tools at Halewood. This gives them tighter control over timelines, quality and cost – and creates the space for staff to build deeper technical skills.
Takeaway for leaders: What could you do better, faster, or more flexibly if you had the right capability inside your business?
3. Adapt and overcome: trade challenges and triumphs
JLR recently faced a major challenge when US tariffs on UK-built cars spiked to 25%, forcing a temporary pause on exports. But the business didn’t panic. It adapted, held firm, and working alongside HM Government has has since benefited from a new UK–US trade deal that now allows up to 100,000 vehicles per year to cross the Atlantic with just a 10% tariff.
Takeaway for leaders: International trade is unpredictable – but with the right mix of diplomacy, patience and contingency planning, you can come through stronger.
4. Improvement is everyone’s job
JLR’s lean philosophy runs deep. From the shop floor to the boardroom, every team member is encouraged to spot problems and improve the process. That culture – where people feel ownership and responsibility – is what gives JLR its edge.
Takeaway for leaders: Do your people feel like they’re part of the solution? Because when they do, you unlock serious value.
5. Investing in the next era
From Wolverhampton to Solihull, JLR is retooling for an electric future. Its Engine Manufacturing Centre is becoming a global hub for electric drive units – part of a wider strategy to future-proof the business and serve the growing EV market.
Takeaway for leaders: Electric, digital, sustainable – whatever the transformation in your sector, the time to invest is now.
Final thoughts
There’s a lot of senior executives can learn from Jaguar Land Rover. Not just in terms of tech, but in mindset. Resilience. Long-term thinking. Smart use of data. Bold but balanced investment.
At HURST, we believe great businesses never stand still – and neither should we.
If you’re looking to sharpen your own operations, rethink your strategy, or just want a fresh perspective on growth, we’d love to chat. Contact us imagine@hurst.co.uk